How Welding Inspection can Save You Time, Stress, and Money.
Table of ContentsWelding Inspection Can Be Fun For AnyoneThe Buzz on Welding Inspection3 Simple Techniques For Welding InspectionSome Known Incorrect Statements About Welding Inspection The 6-Minute Rule for Welding InspectionWelding Inspection Can Be Fun For AnyoneWelding Inspection - Questions
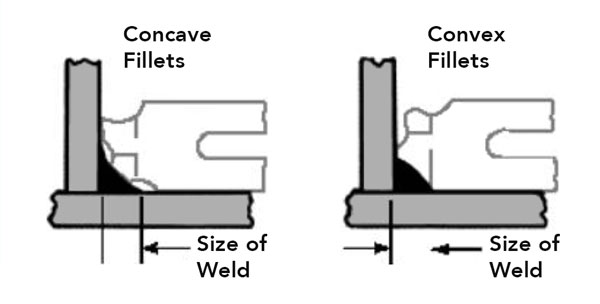
2 Senior Welding Examiner levels with know-how involving ferrous as well as nonferrous products. Our strategy to weld evaluation as well as surveillance It is vital to identify any type of problems with welds before they rise or right after they take place so they can be dealt with as swiftly as possible. Aspect's weld examiners assess the high quality of welds at every step of the fabrication procedure before, during, as well as after welding.
Customers have ranged from exclusive to public and also huge to tiny; the focus is always on maintaining a high standard and also conformity with the relevant code to guarantee that your job has met all of the essential needs be they code, local, business or governmentally enforced policies and also or needs.
The 20-Second Trick For Welding Inspection
Eddy current testing, In eddy existing screening, electro-magnetic currents create an electromagnetic field that connects with the subject, creating localized eddy currents. Changes in stage as well as magnitude indicate flaws as well as can be gauged to quantify size, shape and also location. High frequencies are utilized to measure problems at or near the surface, while reduced regularities can pass through much deeper within the guinea pig.

Numerous qualities of the weld might be assessed during a welding evaluation, some concerning the weld measurements and also others about using gaps of the weld. The dimension a weld might take is essential given that it can straight link to the weld's sturdiness and associated performance, tiny welds might not hold up versus stress applied while in service.
Not known Incorrect Statements About Welding Inspection
These are imperfections with or close with the weld, that can or not associate with their dimension and/or place, block a weld from seminar its made effectiveness. Normally, such interruptions, when are of undesirable dimension or location, are called welding problems and also can likewise occasionally cause very early weld stopping working though the lessening of the weld's durability or though producing stress degrees within the element of the weld. Welding Inspection.
The most fundamental objective is to make a decision if the weld has an appropriate and also top quality for the made program. To be able to access a weld's top-notch, there should be some standard to which its features can be compared to. It is wrong to try and also access a weld's quality in the absence of some details authorization needs.
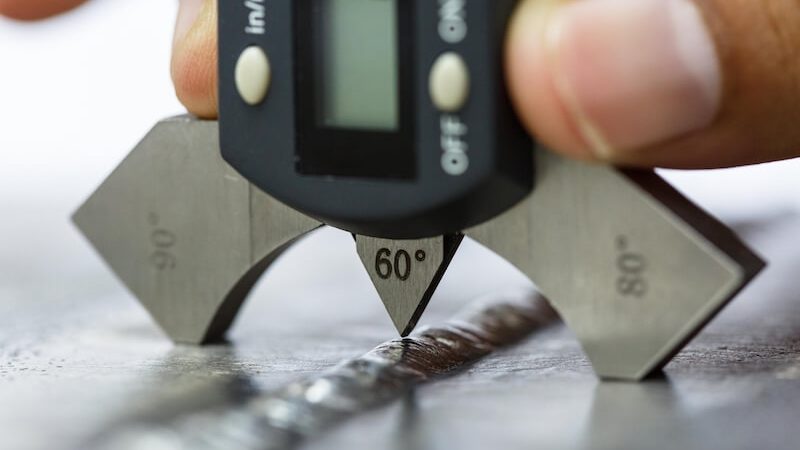
About Welding Inspection
This technique is performed in a workshop or field while the welding is being done. The important things that are visually examined include the welder's certification, slag elimination, joint prep work, climate condition, current used, as well as condition of the electrode. 2- Magnetic Bit Examining This test is utilized to find any surface area or hardly subsurface flaws in a weld.
Bits of iron are after that related to the magnetic area and if there are any flaws, the bits of iron will construct up around the flaw, which reveals where the defect is and why it took place. 3 Liquid-Penetrant Testing This test will certainly detect defects in the surface area of the weld like porosity and also hairline fractures.
A developer is then used that will certainly show if any type of flaws show up. 4 Ultrasonic Checking This examination is achieved by the use sound vibrations, which are then sent via the welded joint. The signals received on a glass display will certainly figure out if there are any type of flaws in the joint of the weld.
Welding Inspection Fundamentals Explained
5 Eddy Current Screening This examination will certainly show extremely little splits and is completed by the usage of a circular coil that brings rotating currents, which is placed near the weld. The alternating currents will create an electromagnetic field, which will communicate with the weld and also consequently, generate an eddy present.
The resulting impression size is referred to as a solidity measuring table. 8 Damaging Testing This test is a devastating examination that is accomplished by cutting the completed weld into items, this is per the code for origin bend, face bend, tensile test, as well as side bend. It is made use of to find slag inclusion, porosity, as well as navigate here undercutting defects in welds as well as is extremely reliable.
This technique is carried out in a workshop linked here or field while the welding is being done. The important things that are visually inspected include the welder's certificate, slag removal, joint preparation, weather, present used, and also problem of the electrode. 2- Magnetic Fragment Evaluating This examination is utilized to locate any surface or hardly subsurface issues in a weld.
What Does Welding Inspection Mean?
Bits of iron are after that used to the electromagnetic field as well as if there are any defects, the fragments of decision develop around the defect, which reveals where the issue is and also why it took place. 3 Liquid-Penetrant Examining This test will find defects in the surface of the weld like porosity as well as hairline cracks.
A programmer is then applied that will reveal if any type of problems are visible. 4 Ultrasonic Checking This examination is completed by the use sound vibrations, which are after that transmitted with the welded joint. The signals obtained on a glass screen will certainly identify if there are any kind of issues in the joint of the weld.
5 Eddy Current Screening This examination will reveal very small splits as well as is achieved by the use of a round coil that carries rotating currents, which is put near the weld. The alternating currents will certainly develop an electromagnetic field, which will certainly communicate with the weld as well as in turn, create an eddy current.
Little Known Facts About Welding Inspection.
The resulting imprint size is referred to as a firmness determining table. 8 Harmful Evaluating This test is a devastating test that is accomplished by reducing the completed weld into pieces, this is per the code for origin bend, face bend, tensile test, as well as side redirected here bend. It is made use of to find slag incorporation, porosity, as well as undercutting flaws in welds as well as is extremely effective.